丰田节约的生产方式教会了现代汽车工业如何有效地制造汽车,世界汽车工业现在一窝蜂地学习成为丰田汽车那样的汽车公司。
但是学习丰田的什么?
其实我们中的每一位专家、教授、讲师和经理人,只要读过丰田的书籍,就都知道丰田模式的目标和远景,也就是说,我们知道要做成丰田的样子应该是什么样的。但是我们中又有多少人知道,要达成这个“样子”,应该经历哪些改革之道路?需要如何的步骤?需要如何的基础?
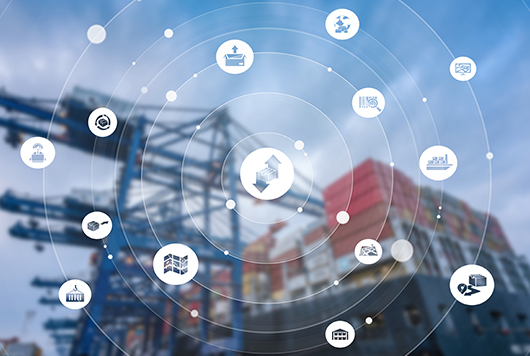
我们更多的时候是说:“我们有很多具体情况,无法做到丰田的这个样子!”
我们先看看即使是今天的丰田,他们又是如何做的?
在过去的5年里,丰田通过渡边捷昭为丰田节约了100亿美元,保证了丰田近年来利润额的持续上升。进一步把丰田"成本控制"推向一个高潮,跨国汽车公司的成本战正式拉开了序幕。
目前,丰田的纯利润已经超过了"底特律三大"的总和,市场资本总额更是远胜三者,在过去的25年中,丰田的产量足足翻了7倍,以至于美国《商业周刊》发出"汽车行业正被日本统治着"这样的惊叹。这一切,得归功于丰田一直推崇的精益生产
我们也在做精益生产!我们也做了看板管理!我们也作了拉动模式!
我们也作了JIT意识提升!(大家一致认为确实需要推行JIT!)
我们也作了拉灯、灯板与停线模式!我们也作了“一个流”!……
可是,我们的精益生产是如何的呢?首先需要问一下以下几个问题:
丰田的物料包装非常的专业化、单元化、标准化、一体化,我们的物料是不是也有过包装问题的考虑?而现实是不是经常是各有特色,奇形怪状,标准不一?我们是不是经常司空见惯?
丰田的物料进厂不用检验,这使得他们的物料通过率非常的高,当然物料周转就非常的快,也就无所谓考虑检验周期和相关的扯皮了,我们的物料是否都需要检验?据笔者的调查,95%以上的企业都需要检验!虽然未必是全检。但是,就这个过程就足够制约你的2天的库存了! 即使在整车厂的配套厂也是一样的,更何况是其他行业的其它工厂呢?我们都在学习丰田,检验这一点,丰田就没有教过你?你怎么学习?难道也能够和丰田一样,免检?
每一次,当我听到人们介绍说“我们公司使用了看板”的时候,我都会问“你们的看板是如何计算的?是否有过丢失的情况?”得到的回答都是肯定的,“如何计算不知道,需求拉动吧;倒是,经常丢失!”于是我就在想:“到底目的是做看板还是做别的?” 丰田今天的看板的概念,已经完全不是专家们在书本上介绍的那个样子了,而是灯板、电子看板、拉灯等,关键的是他们的信息管理系统非常的细致而系统化,各个时间点和数量控制的非常严格而准确。我们的信息系统呢?主要是通过ERP/MRPII,不是有调查和统计说了吗?80%是失败的!笔者并不认为软件的失败就是软件的问题,其实看看我们的包装、仓库库位的规划、操作流程、填写的单据、物料进出货数量的精准性、输入的准确性等等,我们就不难理解,为什么很多企业ERP上线了几年了,至今还在使用手工帐的现象了(而且盘点出现盈亏的时候,他们还居然更相信手工帐!这不能不说是软件的悲哀!),我们更不难理解,软件是一个标准的产品,可是你不按照软件所需要的基础工作和执行力来满足软件的需要,软件的失败怎么可能避免?软件都失败了,看板仅仅是一个工具,虽然我们做的非常的漂亮,但是,又怎么能够承担如此之重要的责任?于是,内行的人,扼腕叹息;外行的人呢?“这个软件真烂!”这就是评价!即使是顶尖的软件也照样有过这样的待遇!何况没有任何品牌的看板呢?
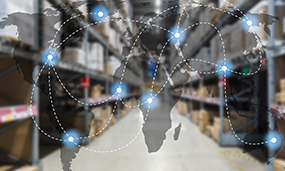
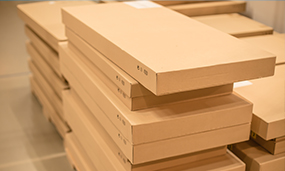
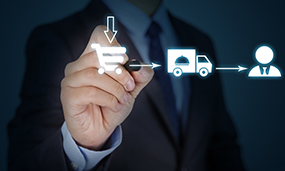
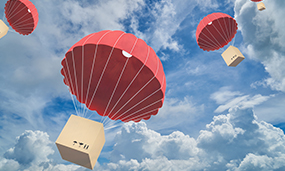
我也经常看到人们在说需求拉动,但是,由于配送能力上不去,或者说根本就无法作细化(细化到每一天的每一个小时甚至是每分钟)的生产排程,再加上物料的单元化无法解决,只好明天的物料今天下午下班前准备好,事先送到工位旁边或者车间暂存区,待到使用的时候,再由操作人员走过去取用,美其名曰“物料超市”。于是车间空间问题、操作人员的走动问题、假停线问题、尾数问题等等,就都出现了,说起来这也是拉动啊。可是丰田的拉动,其实是真实的根据实时的需要,一个单元甚至一个一个的传递的,绝对不是一天一天传递的,由此,我们看到的很多“拉动”的企业照样要问一个问题:“为什么我拉动了库存还是那么高?” 并且为此还和咨询师们争论,直到他们将脑袋在桌子上撞上几个包才罢休。其实答案非常简单:“因为你将仓库提前一天搬到车间了!”